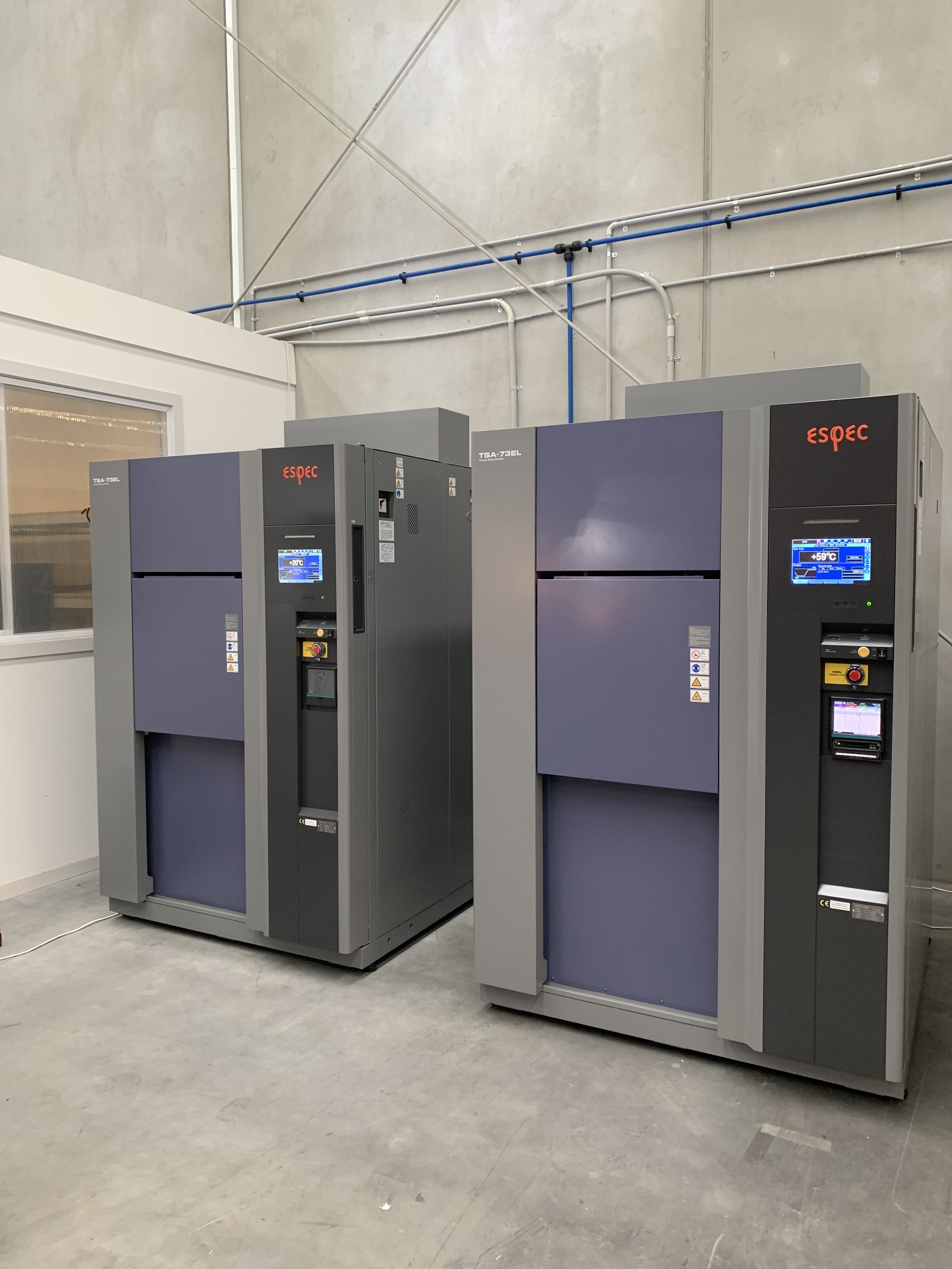
Thermal Shock causes differences in expansion & contraction rates of the materials under test. Stress is also generated by differences in the heat capacity and the thermal time constant of each component element of devices.
Applying these stresses repeatedly leads to cracks and rupturing.
The repeated action of stress causes accumulation of material fatigue, sometimes leading to rupturing at a lower strength than the static strength. Repeated stress can also cause bonded parts to crack, coatings to peel, and screws to loosen.
Thermal Shock Chamber (Air to Air)
A modern take on Air-to-Air Thermal Shock Chambers - the specimen stays still whilst zones are switched using dampers. The TSA series is designed to evaluate reliability of test specimens by rapid change of the air temperatures from hot to cold repeatedly by opening and closing of damper in a single test area.
Thermal Shock Chamber (Large Capacity)
Large format thermal shock testing caters towards full assembly tests on items like lithium ion battery packs for the EV market, and complete sub-assemblies for the defence industry. Designed to evaluate reliability of test specimens by rapid change of the air temperatures from hot to cold repeatedly by opening and closing of damper in a single test area.
Thermal Shock Chamber (Liquid to Liquid)
Liquid to liquid thermal shock testing applies thermal shocks to test samples by alternately immersing them in a high- and low-temperature liquid medium. Since a liquid is used as the thermal medium, this type of testing can attain a sharper temperature variation rate than air to air thermal shock testing.